青森の基幹産業を土台から支える
りんご生産者から圧倒的支持を集める
老舗段ボール企業のAI受注予測への挑戦
森羽紙業株式会社 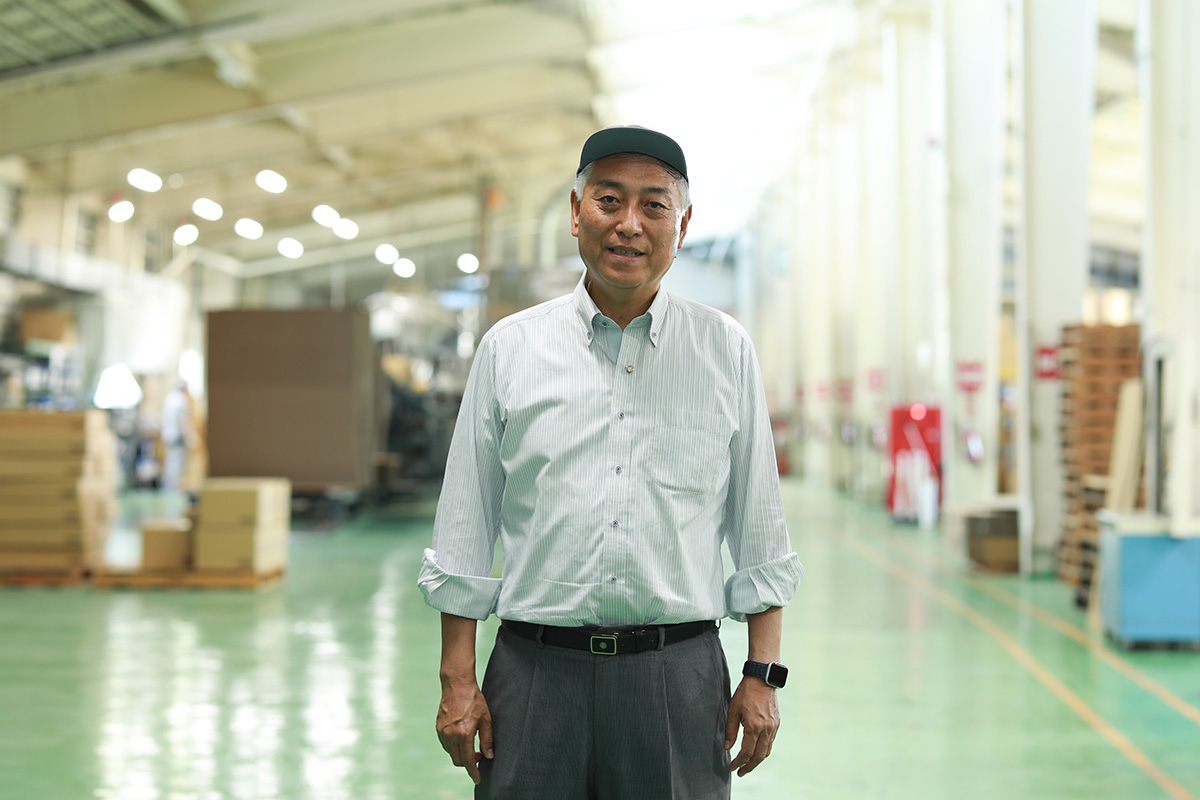
昭和46年創業以来「いのちをはこぶやさしい段ボール製品を皆様に」をコンセプトに、青森の一次産業を支えてきた森羽紙業株式会社。青森のみずみずしいりんごを、みずみずしいまま、より遠くへ、より多くの人々にお届けするため取り組む、業務のデジタル化への挑戦について、代表取締役社長の長谷川通氏にお話を伺いました。
- 事業内容
- 段ボール製品製造・販売
- 協力企業
- 東日本電信電話株式会社
生産現場の心臓 スケジューリングの最適化を
DXに挑戦するきっかけについて教えてください。
段ボールといってもたくさんの種類があり、たくさんの工程を踏んで出来上がります。長さ、幅、深さ、入れるものの重量、段ボールの厚み、紙色など様々あります。使用する機械も同様、箱を製函するグルーマシンと呼ばれるものだけでも3種類、紙を決まった形に切リ抜く抜き型機が2種類、そのほか機械に入らないような大きい箱を作るステープラーや、片面段ボールを作る機械など用途によって使用する機械が違ってきます。加えて、作業工程は、段ボール箱の材料となる段ボールシート制作の行程を経て、印刷・製函の工程は7行程にもなります。
様々な種類、様々な形状、様々な工程で作られる段ボールの製造工程では、急な変更やお客様のご要望に応えられなかったことも多く発生していました。やむを得ず生産予定にずれが生じた場合などは、作業が21時や22時ごろになることもあり、従業員に負担をかけることも多かったと思います。
当時からその業務フローに限界を感じていました。そこで、生産データの管理や生産ステータスの確認などの改善で、生産スケジュールの最適化を図ることはできないか、従来のシステムをより効率の良いものにするためにどうすればいいのか考え始めたのが2015年ころでした。
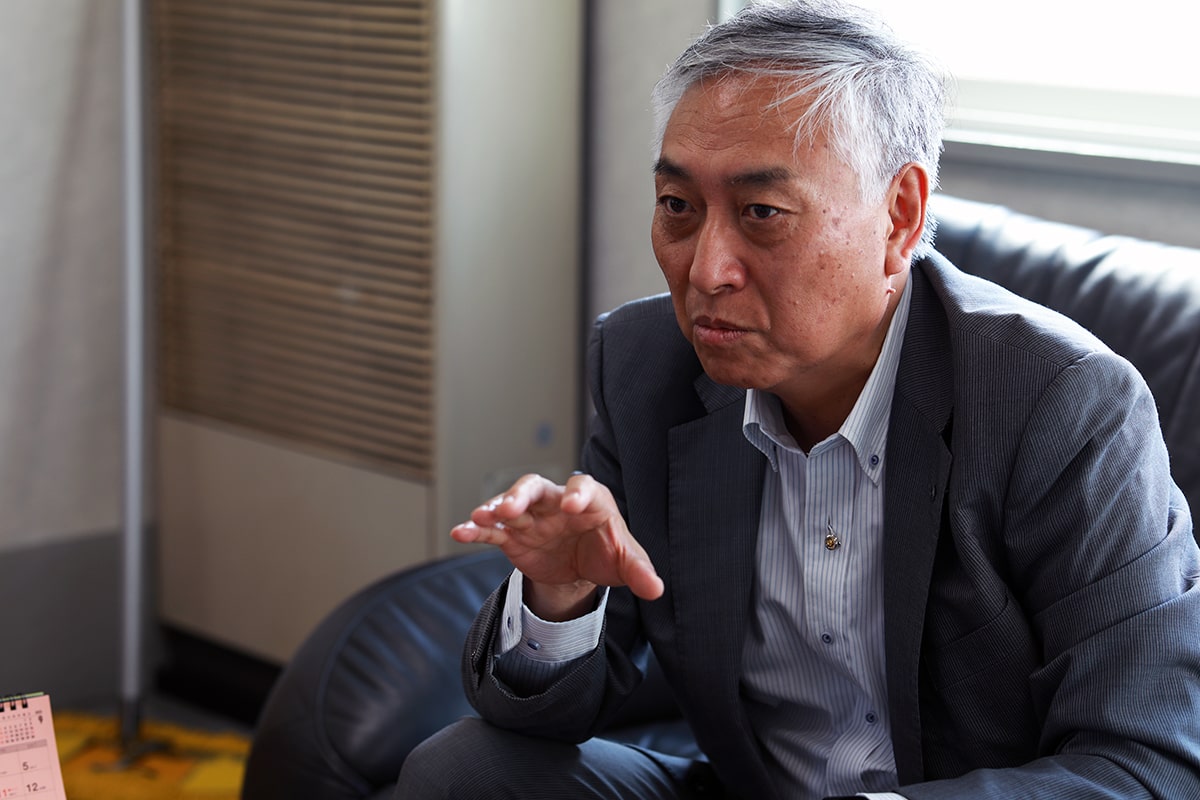
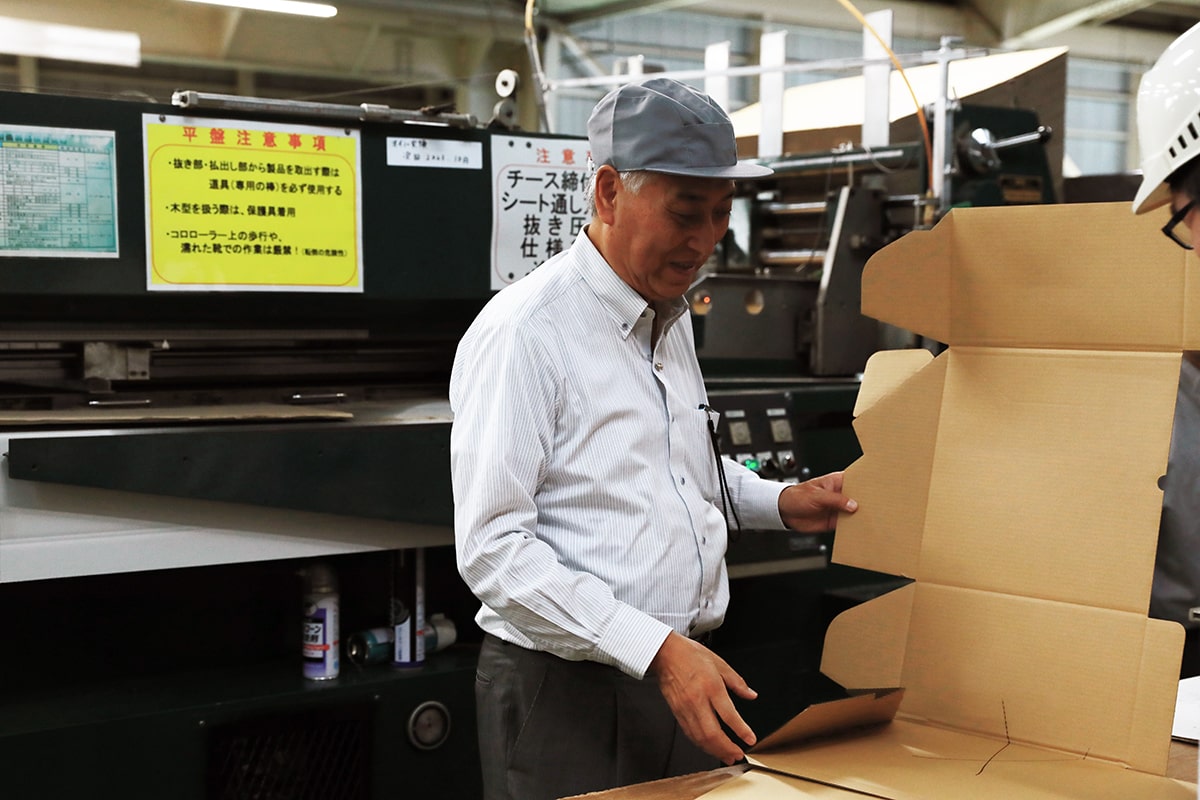
より効率的なやり方はないか 汎用システムからの脱却
具体的にどのような課題があってシステム導入に踏み切りましたか?
まずは、機械ごとの生産量の見える化が必要だと考えました。
先ほどご説明した通り、一言で段ボールの制作といっても様々な行程があり、行程ごとに違う機械で製造しています。そのため、リアルタイムで機械ごとの稼働状況が把握することができれば、機械の運転時間も把握することができ、工場を効率的に稼働させることが可能になります。さらに、生産予定の自動化も実現できれば、今よりも画期的な業務改善が見込めると思いました。
そこで、まずはできるところから始めようと、汎用システムの導入に取り組みました。生産量やステータス、スケジュールなど手作業で行っている作業をパソコンで管理できないかと。
実際に汎用システムの導入をしたところ、システムは止まることがなく安定稼働して便利にはなりましたが、汎用システムではスピードが遅いということや、どうしてもかゆいところに手が届かないという問題が出てきました。そして、運用していくと、実はそのかゆいところが最も重要なポイントであることに気づいたのです。
システムに求める条件はどのようなものでしたか?
「よし、ここからが本当の挑戦だ!」という感じでした。とにかく、汎用システムから抜け出そうと。新しく導入するシステムは、IT企業に相談もしていたのですが、自分でも最適なシステムを探しました。
新しいシステムに求めたことは、工場にある機械と管理するパソコンの連携強化です。間接部門と生産現場の連携による効果的な工程管理によるリードタイムの短縮が必要だと考えました。具体的には「機械ごとの各種分析」と「生産予定の変更のし難さ」の解消です。システムの調査にはだいぶ苦労はしましたが、弊社に適したシステムが見つかったと思ってます。
段ボール製造業向け 基幹業務システム CBOX(シーボックス)
生産管理ネットワークシステム FACNET(ファクネット)
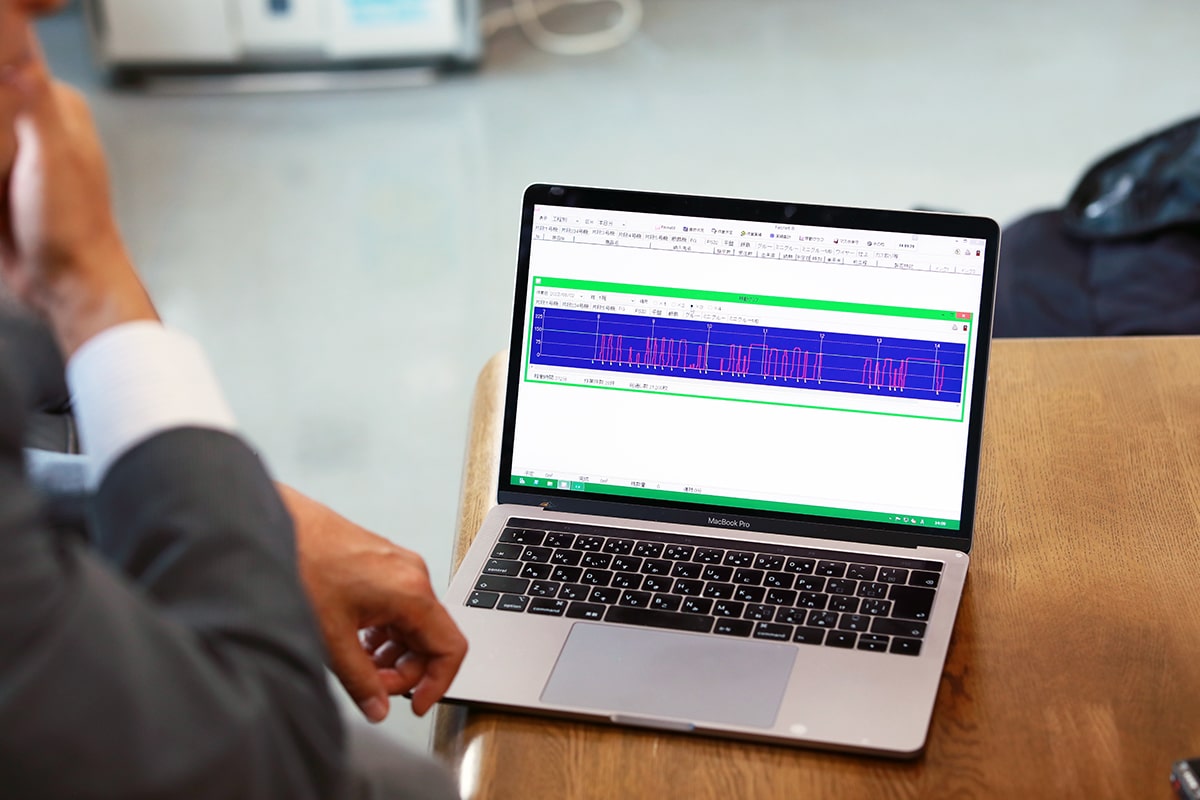
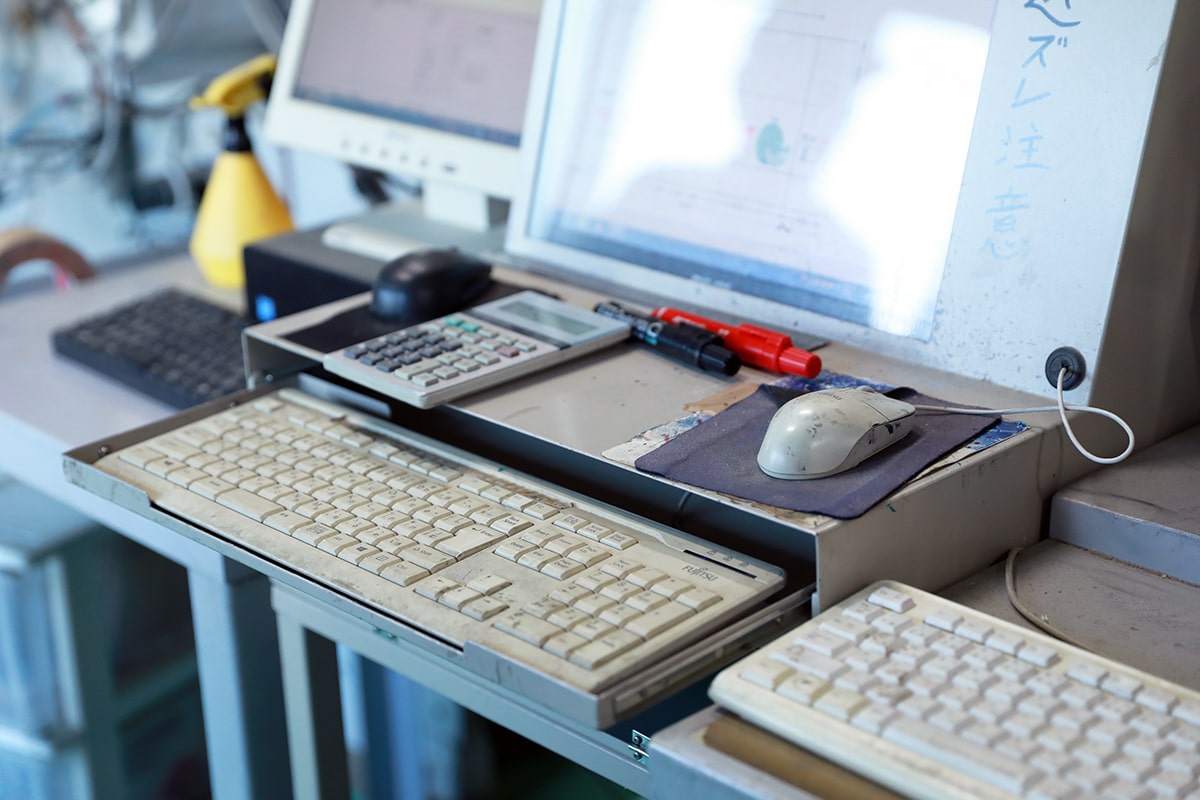
スタートで諦めかけた3万を超えるマスターデータの作成
DXに取り組む際に遭遇した困難について教えてください。
まず取り組むべきは関係者の説得でした。
独自システムではないですが、ソフトウェアを購入して弊社用にカスタマイズするので、やはりそれなりにコストはかかります。その調整、説得が必要でした。そしてもちろん従業員への説明ですね。普段の仕事にプラスしての業務なので。本当に従業員のみんなには頑張ってもらったと思っています。一番大変だったのが、マスターデータの作成です。
弊社では多種多様な段ボールの取り扱いがあるので、そこにはひとつひとつ違った図面と、その図面の情報が存在します。立ち上げの段階で2万以上はあったと思います。システム導入するまでは図書館の蔵書管理のようなイメージで管理していました。種別ごとに分類し、棚割して、ラベルをつけてというように手作業です。そのすべての製品マスターを作らなければならないわけです。一旦できてしまえば、あとは新規で追加するものだけ作ればいいのですが、スタートは地道に作っていくしかないわけです。従業員には、「申し訳ないけど頑張ってくれ!」という、そんな思いでした。
マスターのデータ作成・移行だけで、1年以上の時間がかかっています。おかげさまで現在は35,000を超える製品マスターデータが登録され、生産ラインの自動化に大きく貢献しています。
このように、今のシステムはさまざまな努力と理解によって、やっと今の形になったという感じです。従業員には本当に苦労かけました。
具体的な成果や効果はいかがですか?
機械にセンサーをつけて連動しているので、リアルタイムで状況確認できることが大きいです。やはり導入前は、紙ベースの数値を機械に直接打ち込んだりしていたので、当然ミスも多くありました。
システム導入後は、生産ラインと管理するパソコンが一瞬で繋がって、数値化されたものがデータとして自動に登録され、もちろんその情報がシステムに残る。日報も自動で出来上がり、人的エラーも減少し不良品の減少にも繋がっています。導入によるメリットは非常に大きいです。
お客様に段ボールを提供する納期も早くなったと思います。在庫を足したり引いたり、コンピューターが一瞬でやってくれるので。材料の発注も早くなりました。導入前の発注業務は、1日の作業が終わって、在庫確認して、手作業で足し引きしたものを入力していく必要がありましたので。その他、特急作業が発生しても迅速に処理できるという大きなメリットもありました。もちろん、残業時間の削減や生産性の向上につながっています。苦労はありましたが、結果的にメリットのほうが、はるかに大きかったです。
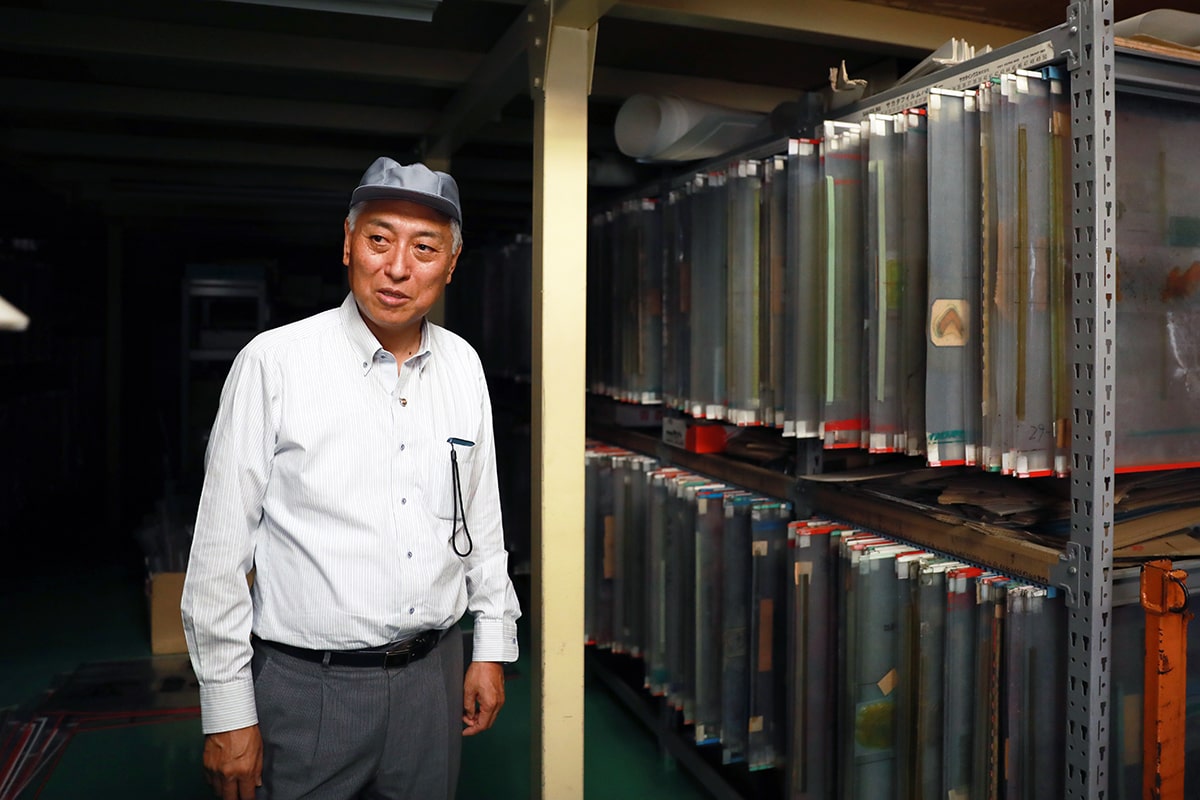
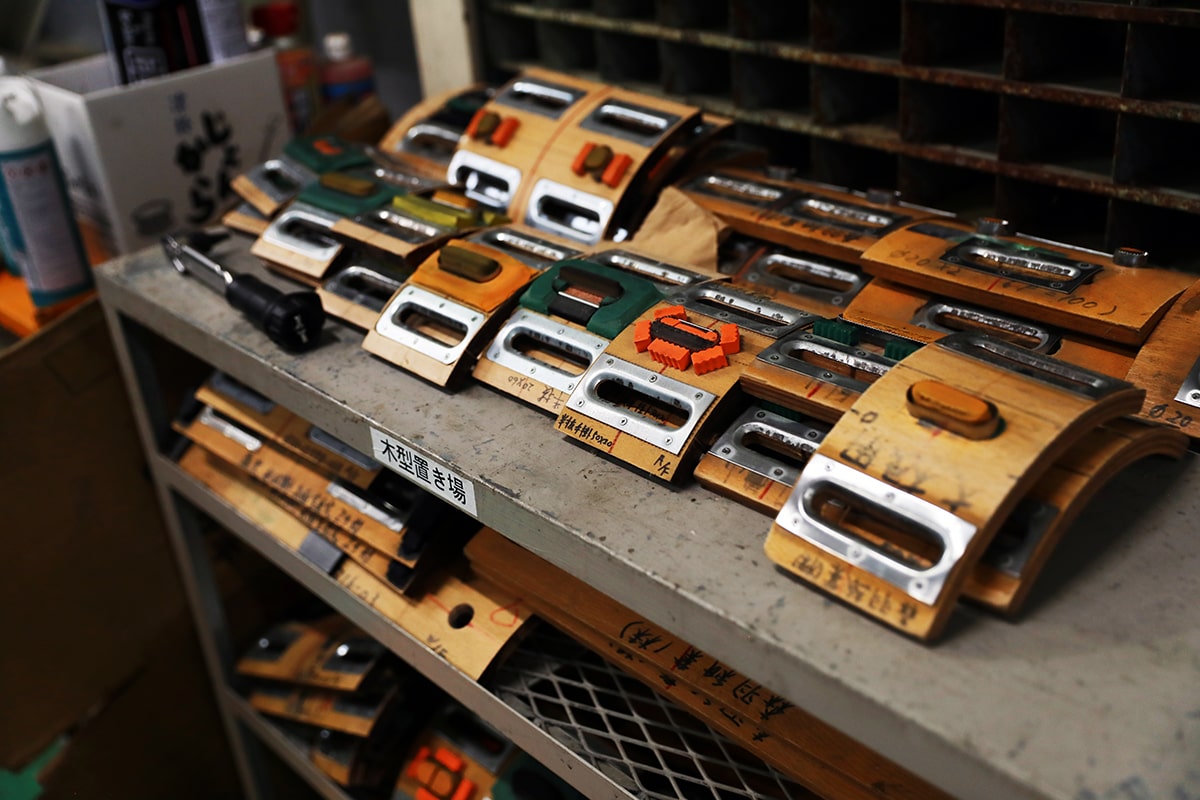
新たな挑戦!次はAIを活用した受注予測システムの導入!
実際にDXに取り組み、社内に何か変化はありましたか?
間接部門のスタッフも、生産現場スタッフからもシステムを導入して良かったという声はいただいています。自分自身も、各機械と繋がったことで、ここまで効率化が図れるとは正直思っていませんでした。これはやってみて初めてわかりました。おかげさまで、会社としてもより生産効率を上げることに積極的に取り組めるようになりました。
今回のシステム化よって、次はどういう風にしたら生産効率が上がるかっていうことを全員で考えるきっかけになりました。作業効率を上げるために、リードタイムを少なくするためにはどうすればいいのか。1人でいろんな行程を処理できるようになることで、より効率的に工場が回るということも、今回身をもって全員の共通認識として持つことができました。
今後の展望や、これから取り組みたいと考えていることを教えてください。
同じことをやり続けても進歩はないので、自分にも従業員にも、常に問題を投げかけるようにしています。毎日同じことをやるだけではなく、今までと同じことでも、角度を変えて、別の切り口から業務を見るようにして、時には従業員とのコミュニケーションをとりながら考えるようにしています。
同じことをやっていても、競争に勝てないと思っています。勝てなくてもいいので、いろんなことにチャレンジしていきたいと思ってます。でも、これは絶対に1人ではできません。私含め、従業員みんなでチャレンジしていかないとダメなんです。
次のステージに上がるために、今はAIを活用した受注予測システムの導入に向けて取り組んでいます。
最後に、AIを活用した受注予測システムについて教えてください。
AIの活用は、弊社にとってハードルが高いと考えていましたが、たまたま青森県に相談する機会があり、IT企業とのマッチング支援を実施していると知りました。県の紹介で数社との打ち合わせ後、東日本電信電話株式会社さんより、弊社の思い描く受注予測を実現できるかもしれないと回答を頂き、取り組んでいるものです。
段ボールの受注量の予測は、現在は生産者からの聞き取りや経験則に基づいて、今後の受注量を予測し段ボール箱を生産しているものですが、その作業に膨大な時間を要しており、その課題をデジタル技術で解決したいと思っています。
そこで、天候データ、市場出荷データ、顧客データを活用し、AI技術で受注予測を行い、実装に向けてシステム構築を進めています。
弊社のDXは現段階ではまだ理想の4割程度。それでもこのAI技術の受注予測が実装できれば、おそらく9割近くDXが達成されると思っています。
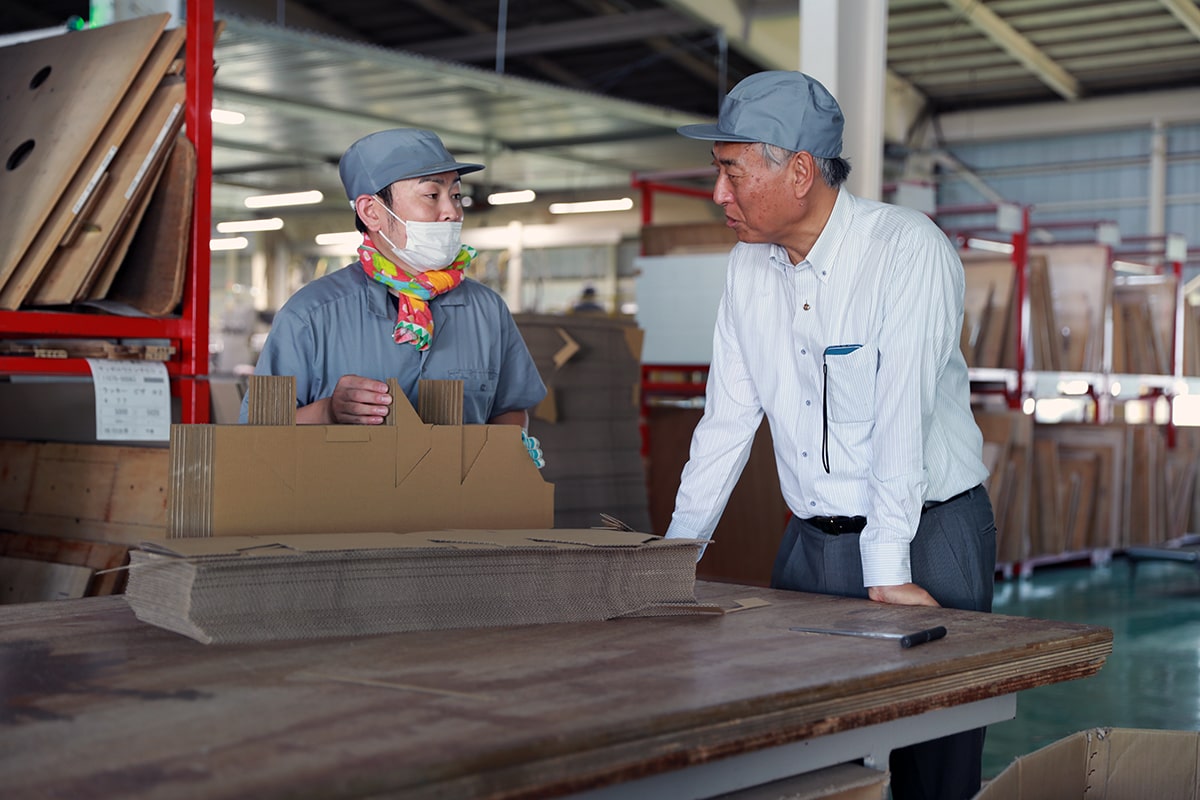
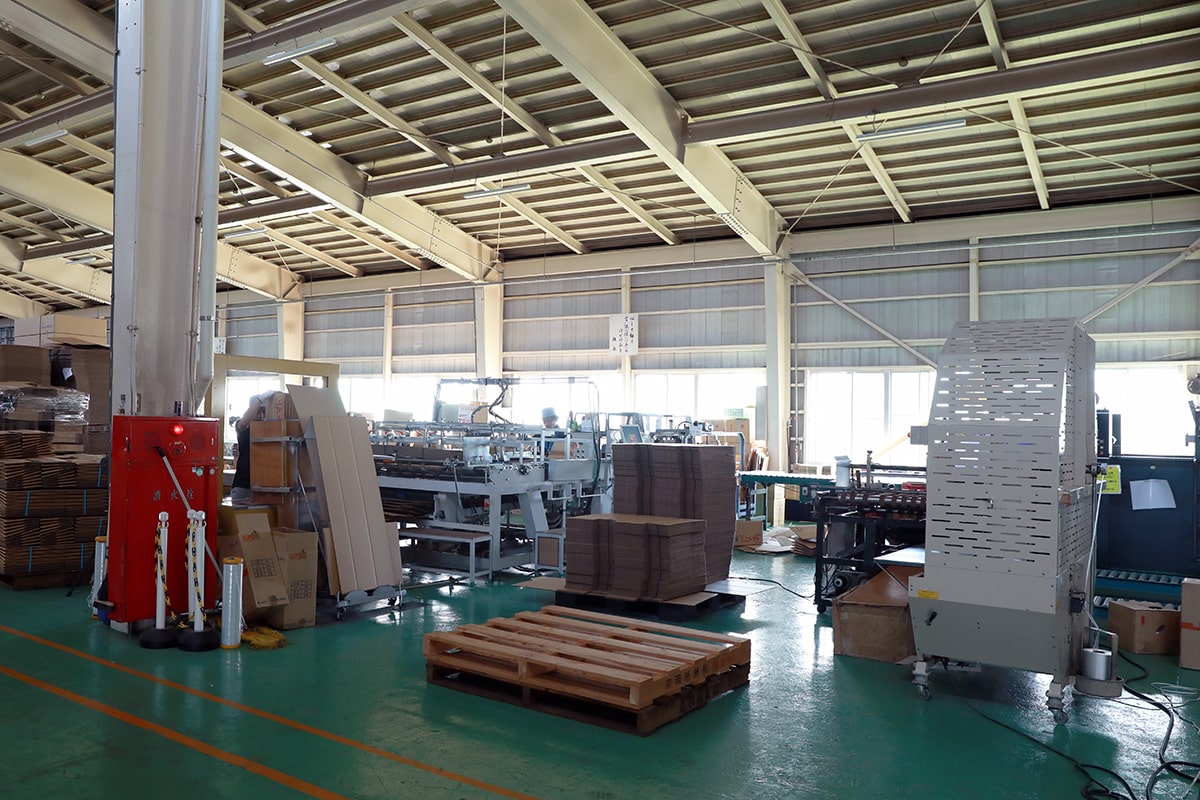
DXで得られた効果
課題
- 機械ごとの生産量の見える化
- リアルタイムでの機械ごとの稼働状況
- 生産予定の自動化
- 生産予定の変更のし易さ
- 機械ごとの各種分析
効果
- リアルタイムで機械の状況確認が可能になった
- 秒単位の生産日報
- 紙ベースの図面の廃止
- 生産日報のデジタル化
- デジタル化による分析の効率化
森羽紙業株式会社
所在地 | 〒037-0015 青森県五所川原市姥萢桜木28-1MAP |
---|---|
TEL | 0173-35-2646 |
URL | https://www.iihako.com/ |